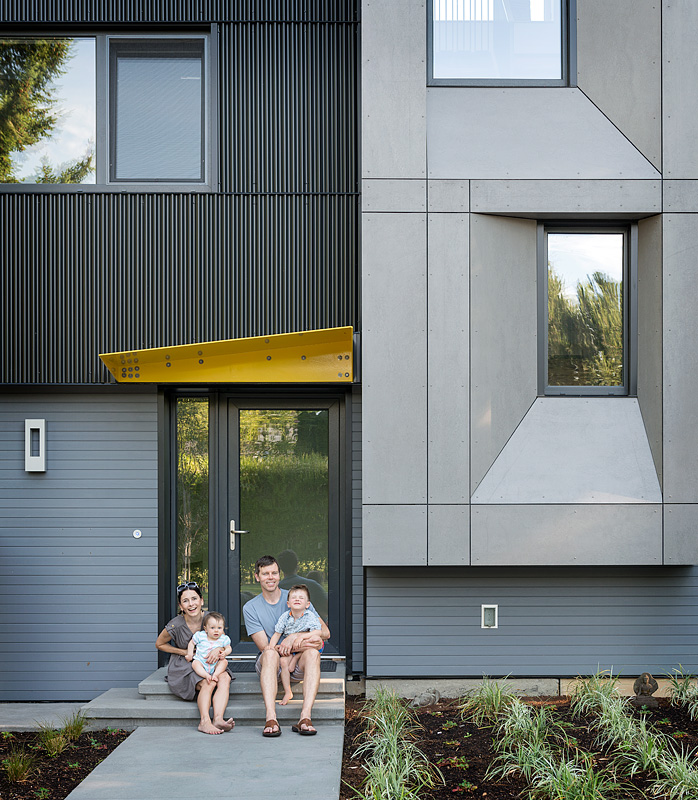
Seattle is among the epicenters of the growing passive house movement
BY: SEAN MEYERS | Updated: November 3, 2021 | Seattle Magazine
In 2013, Sloan Ritchie chose tony and traditional Madison Park as the launchpad for an ambitious experiment in building science.
He and his wife, Jennifer, deliberately selected a bold exterior design for their statement home, to which neighbors turned up their collective noses.
One went so far as to tell Ritchie he didn’t like what he was doing with the home. Ritchie, an environmentalist, later wished he had replied that he didn’t like what the man was doing with his furnace.
“I feel that we, as Americans, are grossly overconsuming resources. It does not happen in a vacuum,” says Ritchie, whose home was the first in Seattle built to certified Passive House Standards.
The neighbors came around when they learned more about passive house technology, and so has Seattle, which is an epicenter of a burgeoning move-ment that was launched in Germany in 1991 and is widely deployed throughout Europe.
Proponents describe passive house technology as one of the last great chances to mitigate the damage of climate change, as buildings account for an estimated 40% of all CO2 emissions. Heating and cooling inefficiencies create most of those emissions.
A passive house is simultaneously tight as a tick and snug as a bug in a rug. Thoughtful design, high-tech windows, an impenetrable cloak and triple insulation produce a structure that uses 80% to 90% less energy than the average home, and 50% less than current Washington energy codes for new construction.
A radio frequency engineer by training, Ritchie switched channels to a career in construction. He was dismayed to learn that the vast majority of Seattle’s builders don’t exceed minimum energy code requirements.
As owner of Seattle-based Cascade Built, Ritchie went on to construct the city’s first passive house-certified townhome. The company was also general contractor for 32-unit Pax Futura, the first apartment building in the city certified by the Passive House Institute U.S., or PHIUS.
Cascade Built recently completed Ellie Passivhaus at 320 Queen Anne Ave. N., the largest passive house-certified project in Seattle to date.
Ritchie was the lone builder testifying in favor of the improved energy codes passed by the 2018 Washington Legislature.
A wide range of building trade organizations and lobbyists lined up against him. Those newer codes, which improve energy efficiency by perhaps 10%, won’t go into effect until 2024, and only then because Gov. Jay Inslee intervened and forced implementation, Ritchie says. “I’m happy the new requirements were passed. It’s something. It’s significant. I just hope it’s not too late.”
Ritchie’s home sips store-bought electricity with its pinky in the air. Such is the efficiency of a passive house that solar gain, body heat, light bulbs and ordinary appliances produce much of the energy required to make it toasty on even the most disagreeable winter eve.
The home is sealed for freshness. In the winter, a mechanical recovery system draws heat from evacuated air and mixes it with fresh incoming air that is distributed throughout the house via small, unobtrusive vents. The process is reversed in summer to cool the home.
Mechanical systems remove moisture from Seattle’s humid climate, creating a mold-free environment. Passive house denizens report a variety of other health inducements, ranging from reduced joint pain to a remission in asthma.
“I haven’t had trouble with my allergies since I moved in here,” says Ritchie, who discovered another benefit when he inserted a special filter to eliminate wildlife smoke last year.
Ritchie built pioneering Green Built and Platinum LEED homes before settling on a passive house for his family. He began construction with typical 2×6 wall studs and attached I-joists to create a 15-inch cavity for insulation.
From the builder’s standpoint, much of the challenge is in learning how to use various materials such as special sealants and gaskets to ruthlessly terminate air penetration and other thermal bridges. A passive house is 10 times less drafty than most new homes.
That may sound daunting, but Ritchie insists it is not a complex system. Fear of the unknown is the biggest roadblock to the technology being more widely accepted.
“The barrier is in the mindset, having the courage to do it and stick with it,” Ritchie says. “The technical challenges are not that great.”
Cascade Built is careful to certify all passive house projects.
“Green washing” is a problem in the construction industry, with contractors who have done little or nothing in excess of minimum code making false claims, Ritchie notes. “The term du jour might be ‘ultraefficient’ or ‘super green.’ You also see projects advertised as ‘built with passive home principles,’ but when you ask for details, they can’t come up with anything specific.”
Interest in passive house construction is “growing exponentially,” says Tadashi Shiga, founder of Seattle-based Evergreen Certified, which provides third-party verification for PHIUS. “It’s really booming. There are five multifamily projects going up in Seattle right now.”
In addition to green building support services, Evergreen conducts the fog-blower door and infrared camera testing necessary to certify that a building’s envelope is truly sealed. Demand is such that the firm recently opened a second office in Tacoma.
Developers can receive numerous incentives for passive house construction, including expedited permitting in some jurisdictions, and lower- and longer-term HUD loan rates, Shiga adds. In Seattle, multifamily builders can win permitting approval for an extra story.
“Passive house is the best way to get to net zero,” says Shiga of Seattle’s 2050 sustainability target.
Most Seattle passive house projects are not yet carbon neutral or carbon positive, in part because space is at a premium, which doesn’t allow for large solar arrays. That may come as new technologies are developed, such as siding and roofing that incorporate photovoltaic capabilities.
Planning is the most critical step in passive house construction.
“Like everything important in life, make sure that you choose the right team,” Shiga advises. “What you don’t want to do is design a house and then say, ‘Let’s make it passive.’”
The quiver of the Passive House architect includes modeling software, building location and orientation, layout, window placement, thermal mass, shading and ventilation. Olympia-based Artisans Group Inc. has designed more single-family homes to the Passive House Standard than any
other U.S. firm.
“Excitement is building. We’ve gone from one to two website inquiries per week to two or three per day,” says Tessa (formerly Smith) Bradley, Artisans Group principal and a pioneer of the passive house movement in the Northwest.
With numerous awards and accolades, her 100% women-owned firm has proven that elegant design and advanced building science can coexist. Many clients are attracted to passive house technology for the reduced energy bills and carbon footprint, but end up enchanted with the unparalleled comfort and sense of well-being that result from envelope-first design, she says.
“It’s kind of like wearing a thick, woolly sweater without having to wear a thick, woolly sweater,” she adds.
Like Ritchie, Bradley is highly experienced with Green Built and LEED construction. But passive house technology sets itself apart.
There are no cold spots in a passive house, even standing near a window on a frigid day. For example, a room with a 14-foot vaulted ceiling registered 70 degrees at ground level and 69 degrees at the peak, Bradley says. The thick shell filters out stressful noise pollution and the ventilation system provides a steady stream of healthy air.
“I hear a lot of comments like, ‘My kid doesn’t have asthma anymore,’ or, ‘I don’t drink coffee in the morning anymore because I wake up more refreshed,’’’ Bradley says.
“We talk endlessly about eating organic and working out, but we spend very little time talking about how the home we live in affects our health,” she notes. “Covid is causing many people to rethink this. We spend 90% of our life indoors. If you did nothing other than live in a passive house, it would improve your health exponentially.”
Many builders were initially spooked by passive house technology, which resulted in some “wacky” bids, she says. As education and experience increase, builders and customers are coming around to embrace the pragmatism, longevity, ease of operation and cost-effectiveness of passive house living.
Several years ago, the country of Belgium made passive house standards mandatory for any new commercial construction,
yet commercial buildings built to passive house standards are virtually nonexistent in the U.S. Passive houses differ from other environmentally oriented building systems, such as Platinum LEED.
“Platinum LEED construction very possibly would be more expensive, as there is a broader approach to environmental stewardship, such as an emphasis on the use of recycled content and native plantings,” says Zack Semke, director of the Seattle-based Passive House Accelerator, founded in 2019.
“With passive house construction, there is a tight correlation between predicted and actual performance, which isn’t always the case in green building systems,” Semke says. “It’s a really powerful way to improve energy efficiency.”
It costs just 3% to 7% more to build a passive house, since many of the required inputs, such as additional insulation, are relatively inexpensive, Semke says. Multifamily structures built to passive house standards cost just 3% to 5% more.
That hasn’t always been the case. Like solar panels, passive house technology is continually becoming more affordable and efficient. Windows and special HVAC systems, previously imported from Europe, are now available domestically.
Each week the accelerator draws 200 to 300 eager builders from around the world for its “Tech Tuesday” Zoom seminars.
“The faster we all learn from each other’s mistakes and innovations, the more rapidly we can make a contribution to climate resiliency,” Semke says. “Policymakers and the public don’t yet understand the magnitude of benefits that are created at a low cost. We don’t have a lot of time to let it play out slowly.”
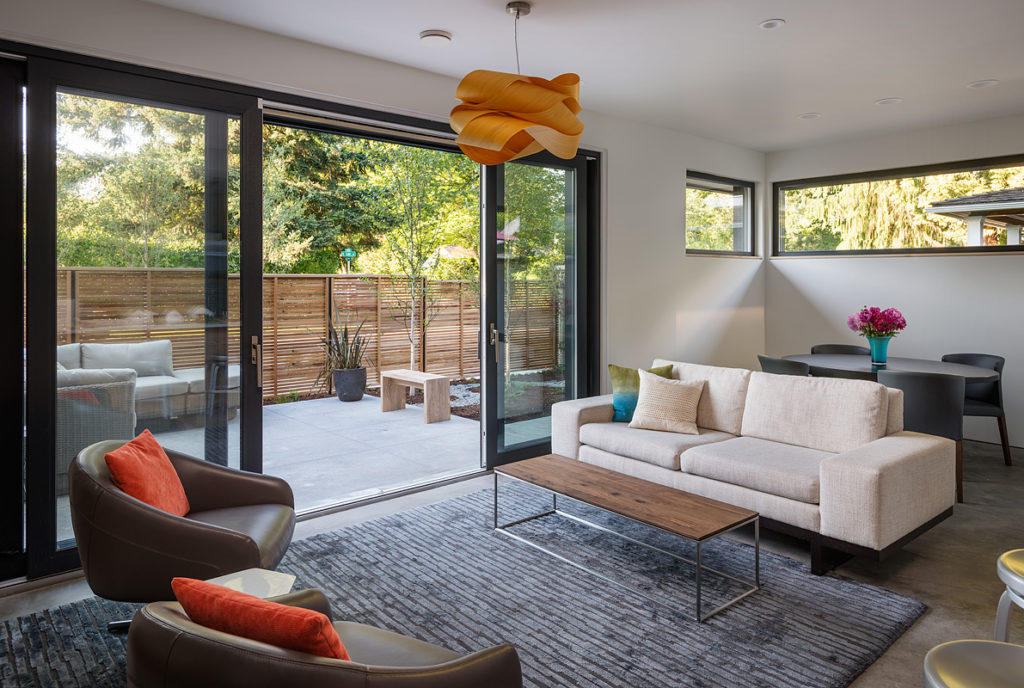